With a 30-year rich history, St. Modwen Homes builds around 1000 high-quality new homes across the UK annually. Its focus on thoughtful design, customer service, and first-time buyers, alongside the highest levels of quality and safety standards, underpin its responsible approach to housebuilding.
Preparing for Part L
In June 2022, a revised version of the Part L Building Regulation was introduced in England and Wales, imposing stricter targets for reducing carbon emissions and improving energy efficiency in new and refurbished homes. A key aspect of the new regulation is the requirement to capture photographic evidence across the build stages of construction to provide proof of compliance with targets.
Specifically, the updated regulation mandates that each plot is built in such a way that it:
- Produces at least 31% fewer carbon emissions compared to previous standards.
- Meets updated U-value targets for walls, windows, and doors.
- Ensures better insulation, airtightness, and eliminates thermal bridging through improved
- materials, technology and construction techniques.
Under the new framework, homes are assessed using the SAP10 calculation procedure, resulting in a Building Regulations England Part L (BREL) report. This report evaluates a home’s efficiency, especially in relation to energy and heating.
Before a home can be completed and occupied, the BREL report must be signed off by the SAP Assessor and reviewed by building control to confirm that it meets regulatory standards.
Ahead of the game, the team at St.Modwen Homes took a proactive approach by deciding early on to implement a digital solution that could be deployed across its 24 sites and 400 users, spanning from the Northwest to Southeast, for projects starting after June 2023.
Paper process to digitisation with Part
With Part L being the trigger, St. Modwen Homes recognised the need to transition its teams from a traditional paper-based quality control (QC) system to a more efficient digital platform, especially given the wide geographical spread of sites across the UK that were using different quality techniques. Centralised digital processes would address paper-based limitations, such as the difficulty in tracking and understanding quality control procedures across different sites, as well as the risk of vital information being damaged or even lost.
Through digitisation, St. Modwen Homes wanted to streamline QC processes for quality assurance (QA), snagging and defect management, audit trails, reporting and overall project management. However, most importantly, they sought a solution that could handle the new photographic evidence requirements for Part L compliance. The company wanted one tool to
do it all.
Finding a solution that could meet these requirements, was the first hurdle. The second was ensuring that the solution would be successfully adopted across multiple sites.
As with any significant change to the ways of working, it was important that the teams were supported throughout this transition. The move to a digital system from the traditional pen-and-paper approach would require a significant cultural shift.
While teams could see the obvious benefits, it would mean a change in how data was thought about, collected, reported, and analysed, and would therefore require time and support to fully transition and implement.
“As a housebuilder, one of our biggest priorities is that when the team or a customer report a snag or defect, that it is reviewed, resolved and closed out correctly. If we’ve got it logged officially and it shows up on a dashboard, people can see its progress every day and track it to resolution. This helps improve overall customer satisfaction.”
Comprehensive quality management
After evaluating several digital solutions for managing quality processes — some more focused on snagging, and others on quality assurance (QA) — St. Modwen Homes selected Zutec to centralise their quality control processes. The initial focus would be on Part L compliance and snagging and defect management.
Already working with Zutec for Digital Handover, St. Modwen Homes discovered that it was the only company offering a Part L solution with a ready-made photographic evidence template which was tried and tested, along with a full quality management (QM) suite that would support St. Modwen Homes’s digitisation journey.
St. Modwen Homes took the decision to implement Zutec, which now enables the company to manage Part L and QM processes, track snags and defects, generate real-time reports, and maintain a clear audit trail of actions, progress, and approvals — a real gamechanger from where they started.
As a cloud-based solution, accessible on both desktop and mobile devices, Zutec can be used in the office or onsite in the field, with or without an internet connection. Templates, forms and workflows provide an environment that takes the pain out of the process of capturing information, sending notifications, managing stakeholders, and tracking progress and approvals.
Those onsite can use a smartphone or tablet to capture data and information, including georeferenced photographic evidence which can be attached to the relevant BREL report.
Drop-down options in the templates and forms make it easy to capture and record photos with the correct associated information across the project, dwelling and location, which is essential for submitting to reviewers and assessors. This simplifies the process of sharing, reviewing and submitting evidence for mandatory requirements such as EPC and BREL reports.
The Zutec platform is also configurable and can be tailored to align with company processes, so every project is streamlined.
Users can set up workflows and notifications so tasks can be tracked, and review points added for assessment, feedback and approvals, as well as where more work needs to be done.
Having a flexible review process means any remediation work required can be done before works are completed. This made Zutec the best construction management software for the job.
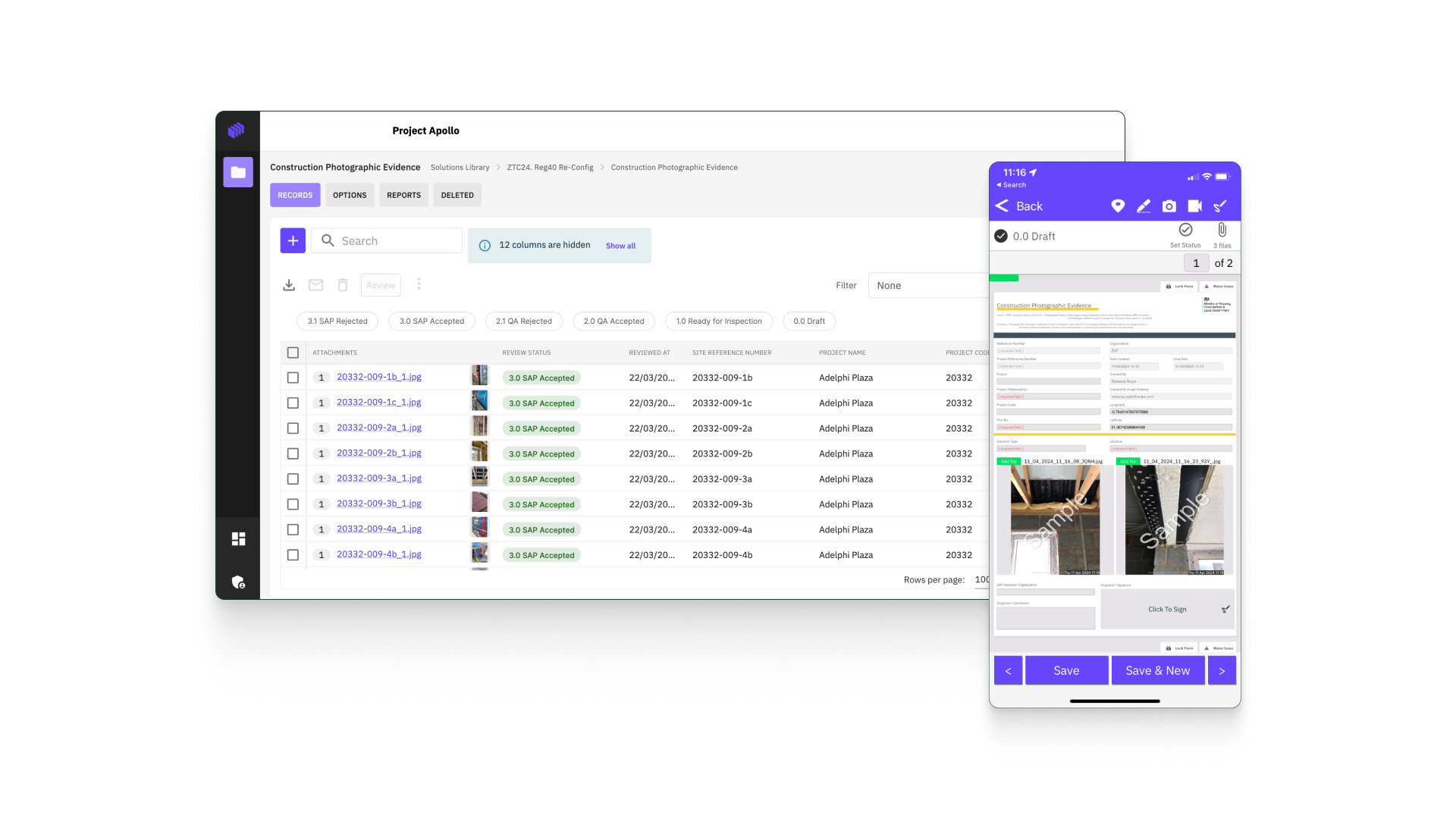
Changing team mindset
Zutec’s experience with housebuilders enabled a smooth implementation of Part L photographic evidence and snagging and defect management. The solution includes a field app for teams to capture photos and data, along with a centralised dashboard for progress visibility and management. The main challenge was ensuring a smooth transition to secure user
adoption.
To facilitate this, St. Modwen Homes appointed “Zutec Champions” at various sites to lead the change. With support from Zutec, Bryn Davies, Quality & Health and Safety Systems Advisor coordinated these champions, overseeing site adoption, training, and workshops to drive digital transformation.
St. Modwen Homes also invested in Zutec’s technical account management (TAM) and support services, conducting onboarding and training sessions, including on-site demonstrations. Regular team meetings addressed issues and captured feedback for improvements.
Despite initial hesitance, the education program highlighted the digital platform’s benefits. Leadership at St. Modwen Homes emphasised that paper processes were no longer viable, especially for managing defects and complying with Part L regulations, which helped gain team support.
A key advantage of the Zutec platform for St. Modwen Homes was its customisable dashboard, allowing easy access to essential data for all users, from site managers to senior executives.
Zutec provides senior management with real-time project data for reviews and reporting, especially during management meetings, enhancing understanding of progress across sites and enabling faster, informed decision-making.
Standout features
Designed to meet St. Modwen Homes’s needs, the tailored dashboard offers insights and analytics, highlighting areas that require attention for quick action. With a single record and an audit trail, the company can identify strengths and areas needing improvement, ensuring nothing is overlooked.
This reduces delays, saves time, and significantly minimises customer issues at plot completion and handover. Site Managers can record actions in the dashboard and assign tasks to team members before moving to future construction phases.
This is crucial for Part L compliance, as photos can be sent to reviewers and assessors at each build stage, allowing for pre-approval and inclusion in the BREL report before plot sign-off. Early detection of issues, such as defects or the need for additional evidence, enables prompt resolution.
By approving photos during construction, teams can avoid costly rework and prevent delays if evidence doesn’t align for plot and BREL report sign-off.
Overall, St. Modwen Homes has implemented seven key QC processes on Zutec and plans to add more in the next 12 months, extending benefits across the organisation. While QC focuses on construction, more internal departments are requesting logins, finding the data invaluable for decision-making and customer support. The company is also considering integrating
health and safety processes into the platform.
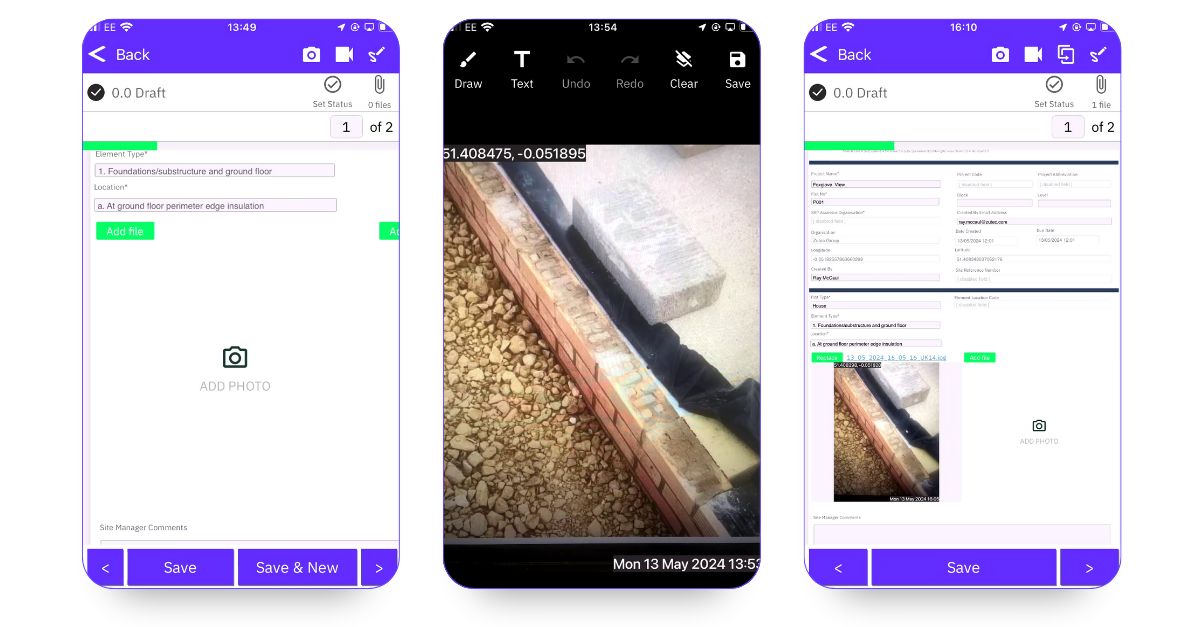
“Now teams can see how much useful data we get out of Zutec, it has hit home the importance of such a solution and is building confidence across the business, particularly with handing over a new home. Instead of simply raising an issue verbally and filling out a paper form as we did before, the information is recorded, tracked and used to ensure better working practices from project to project.”
Conclusion
The integration of Zutec into the company’s quality management processes has been a gamechanger for St. Modwen Homes.
Despite initial challenges and the process of change, the platform has significantly improved the company’s quality control processes, particularly in relation to Part L compliance, and snagging and defect management.
The customised dashboards, ability to generate detailed audit trails, and real-time reports has enhanced accountability, reduced risks, and improved overall project management.
The ongoing support from Zutec ensures that the system continues to evolve with the company’s needs, making it a vital tool in its construction management toolkit.
Additionally, teams can identify, log, track, address and resolve defects and snags more quickly before moving on to the next stage of construction. This leads to significant cost savings, happier customers at completion, and minimising the chances of post-handover problems.
The success of using Zutec as part of its digital transformation highlights the importance of strong leadership, comprehensive training, and the ability to adapt technology to specific business needs.
While more is being done and improvements being made, St. Modwen Homes is now better equipped to manage its projects efficiently and confidently, with a clear focus on quality and compliance.
Download the case study
How St. Modwen simplified Part L photographic evidence and streamlined snagging and defect management.
Fill in the form now and get a free PDF sent straight to your inbox.