In a competitive market, as a housebuilder, being able to stand out through quality management and innovation is key. And, at the same time, meeting new regulatory requirements, like Part L, makes improving housing quality easier said than done.
However many are still relying on manual processes to inspect the standards of work. Having manual operations can lead to disjointed and inefficient process, fragmented communication, lack of visibility and real-time updates or unexpected delays.
All this can result in human error which makes it harder to meet standards or even improve them, especially when working with subcontractors.
Read on to learn more about how new housing regulations and better-quality management are improving the quality of house building, the challenges facing housebuilders and how to take control of quality management processes.
Housing quality
When it comes to new build homes, with the New Homes Quality Board acting as an ombudsman in the UK, for the most part, the quality of housing is generally ok and you can't really sell bad-quality homes. A 2023 Customer Satisfaction Survey published by The Home Builders Federation (HBF), revealed that 88% of respondents said they were satisfied with the quality of their home. However, 95% of respondents said they had reported snags to their builder since moving in.
The problems facing new build homes can be varied, ranging from issues such as paintwork problems or unfinished or poorly fitted fixtures which arise from poor workmanship, to plumbing, such as leaks, inadequate water pressure, or problems with drainage systems. More dangerous issues may include electrical problems resulting from faulty wiring and inadequate electrical outlets, or inadequate ventilation or insulation that can make dampness and condensation occur, leading to mould and mildew growth.
Structural issues such as cracks in the walls, ceilings, or floors, as well as problems with foundations or roof leaks, can be more serious for the people living in the homes, in addition to being costly for the housebuilder to rectify. If left untreated, these problems may lead to more chronic issues down the line.
Why are there problems with the quality of new build homes?
There has been an emphasis on increasing the quantity of housing in the UK which can sometimes come at the expense of quality. Mounting pressure to deliver developments faster may lead to rushed construction, cost-cutting, and inconsistent workmanship. This rush to build can also result in inadequate planning, oversight, and quality control.
On top of this, the UK construction industry has also been facing the ongoing challenge of finding and retaining enough skilled workers to meet the demand for construction projects. Not having enough skilled labourers or reliable subcontractors is also lowering the quality of workmanship and where poor-quality workmanship leads, construction defects will follow.
A significant issue of the skills shortage problem is that we have an ageing workforce. Many experienced tradespeople and professionals are reaching retirement age, and there aren't enough younger workers entering the field to replace them.
Additionally, The UK's decision to leave the European Union (Brexit) has had an impact on the availability of skilled construction workers from EU countries and the resulting restrictions on free movement have reduced the pool of available labour.
Meet regulatory compliance and the highest quality standards
Take control of Quality Management with standardised workflows. Eliminate paper-based processes and collaborate on a single cloud platform and easy-to-use field application.
How to improve housing quality
Not all new build homes experience problems and many housebuilders are taking steps to address quality control, while government reviews and consultations show a commitment to introducing legally binding standards which developers must work to so that they can provide good quality housing.
Housing quality standards
Tighter regulations and building controls issued by the government, such as the Building Regulations 2010, aim to improve the overall quality of buildings, ensure a local authority or approved inspector is carrying out building control services, and provide statutory guidance in Approved Documents that explain how to meet requirements, including how to improve the safety aspects or energy efficiency of buildings (Regulation 40 uplifted Part L). These regulations protect the health and safety of people in and around buildings, as well as future-proofing them.
With the introduction of new legislation such as Part L, which requires evidence that demonstrates all building work and materials used comply with new energy efficiency requirements, building work has to be compiled at appropriate phases of the construction of a property and sent to the SAP Assessor to review and confirm correct construction on completion before work is signed off. To read more about how to prepare for Part L compliance read our blog, ‘Are You Ready for Part L Building Regulations and Photographic Evidence Compliance?’.
Quality management in construction
Quality management in construction is the systematic approach to ensuring that construction projects meet or exceed established standards, regulations, and client expectations. It involves processes, workflows, and practices that aim to deliver high-quality homes while minimising defects, rework, and cost overruns.
Quality management in construction is essential for ensuring the safety, sustainability, functionality, and overall success of a construction project and that homes are built to last.
Building in line with regulatory requirements, building regulations, and industry standards can be a complex undertaking. The road to compliance begins with quality planning which involves defining the criteria and standards that must be evidenced throughout the duration of the build.
Detailed records should be kept throughout the construction process that document all quality-related activities, inspections, and audits. This makes monitoring and evaluating construction activities easier so that housebuilders can identify and rectify any work that fails to meet quality standards and speeds up quality inspections which asses the quality of workmanship, materials, and compliance with design and safety requirements before sign-off.
The effective handover between on-site teams, project managers, and quality inspectors is integral to meeting quality standards the first time around and helps reduce the likelihood of costly errors, rework, disputes, and delays.
What are the challenges in construction quality management?
When speaking to our customers or prospective clients, the challenges they are facing with quality management have some key themes that come up again and again. The most significant challenge is around manual processes. Historically, site inspection work has been carried out using paper-based plot books or gathered on disparate systems.
There’s also a lack of standardisation and consistency with what information is recorded. This means that organisations may have a number of different ways in which they undertake inspections across projects or even on a plot-by-plot basis within a particular site. This makes it incredibly difficult to define what good quality should look like, especially when dealing with multiple subcontractors.
If there’s a different way of doing things on each plot, those carrying out inspections on-site will have to learn new ways of doing the same thing which will slow down overall project progress, can lead to human error and make it difficult to evidence work against compliance.
When information is kept in plot books or disparate systems, information can become siloed causing a lack of visibility across the business. This lack of reporting means that executive teams are unable to view audit trails at the site level or more broadly across a portfolio, and spot patterns or trends so they can intervene early on if necessary or retrieve information at a later date.
With the recent changes to building regulations such as Part L where information and photographic evidence should be provided for each individual dwelling in a digital format, it has become more difficult to show that building work complies with energy efficiency requirements.
As the regulatory landscape continues to evolve as we go forward, it allows little room for inefficiencies and the need for a central repository of information where house builders have complete data ownership will be a must.
How to take control of your quality management processes
The role of digitalisation and having a robust digital strategy and solution in place will help housebuilders avoid some of the challenges mentioned above. By having templated digital forms, checklists and workflows, housebuilders can standardise processes across all projects to drive improved quality, consistent delivery of information and better project outcomes.
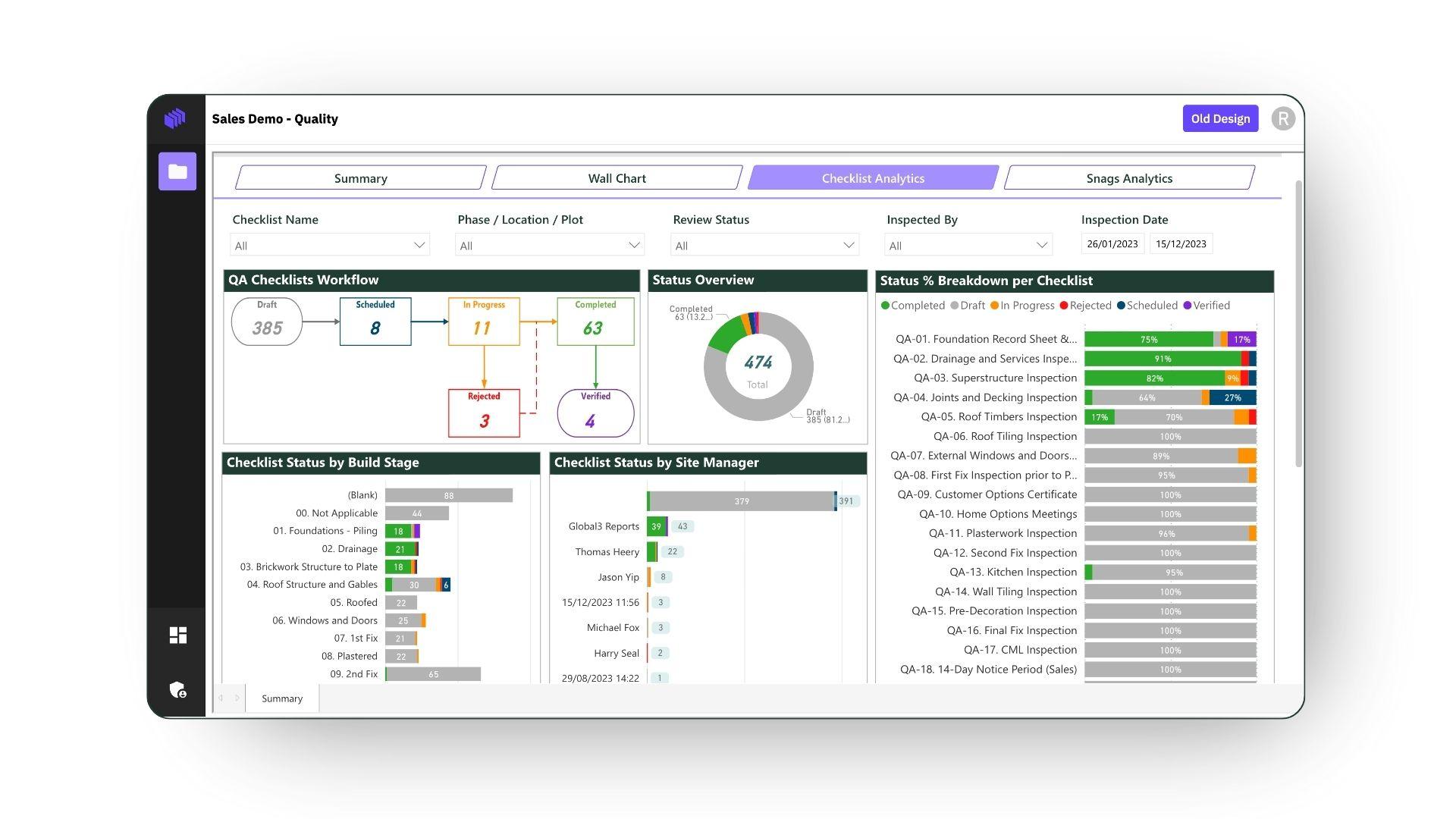
At Zutec, we help housebuilders define their quality processes and build out standard templates working with them to agree on the content of their forms. We’ll then digitise these forms and put workflows and mechanisms in place that meet business needs.
In addition to standardising the delivery of information, it’s important to have an integrated solution where everyone in the business can access information and what needs to be completed. Having an on-site app such as Zutec Field allows teams to identify and close out snags and defects or populate a site diary using a mobile device.
Offline functionality lets users capture data in the field without a Wi-Fi signal, syncing automatically once back in range. This means users can drop pins on 2D layouts or within 3D models, create tasks on the go, or capture the geo-located photographic evidence needed for compliance with regulations such as Part L, from any device with or without a data connection.
At the same time, having a centralised dashboard like Zutec Cloud will provide complete data visibility on project analytics and benchmarking points so management teams can derive value from the information that's being captured on-site and monitor real-time project progress and performance. This offers a 360 view of subcontractor work, where users are able to understand when evidence was captured, and by whom.
Ultimately, more effective oversight results in efficiencies by saving time and money and building right first time, every time. Reliable information empowers teams to make more informed decisions, as well as providing the ability to drive business and strategy decisions moving forward.
To learn more about Zutec quality management for house builders, download our booklet. Or if you need to implement a quality management solution quickly book a demo with one of our experts. We’ll be happy to show you how we can help you take control of your quality management processes.